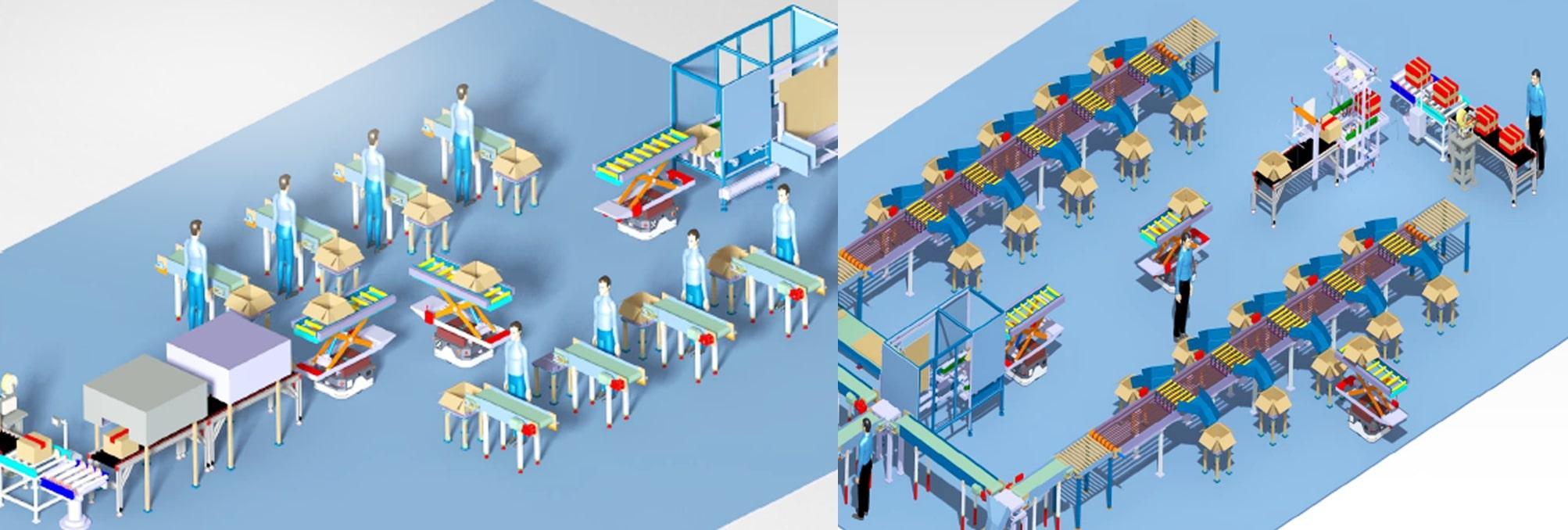
Case Studies
01
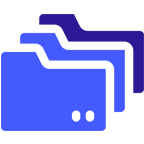
Storage and retrievel system
02
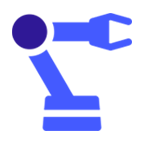
2-Axes Robot for Pick and Place
03
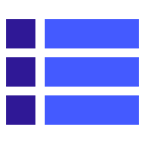
De-Dusting Station
04
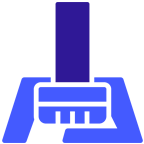
Bearing Cap Robotic Deburring
05
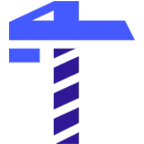
C-42 Gantry
06
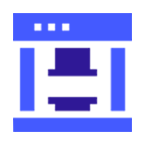
Servo Press
07
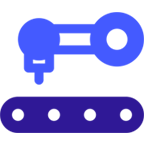
Slat Conveyor
08
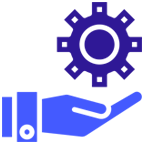
Gear Box Assembly Line
09
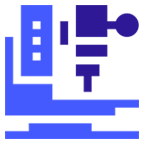
Quench Press Assembly
10
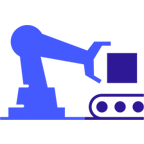
FSP Palletizing
11
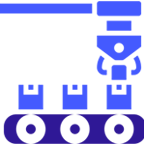
End of Line Packaging
12
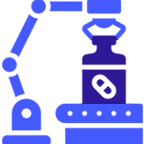
EOL Packaging for a Reputed Pharma Customer
13
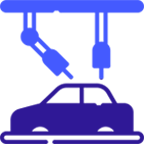
EOL Packaging for a Global Automotive OEM
14
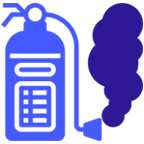
EOL Packaging for a Global Fire Protection System OEM
15
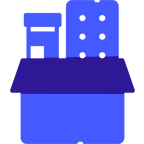
Warehousing for a Reputed Pharma Customer
16
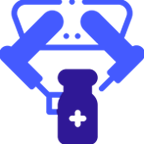
De-Dusting for a Reputed Pharma Customer
01
Storage and retrievel system
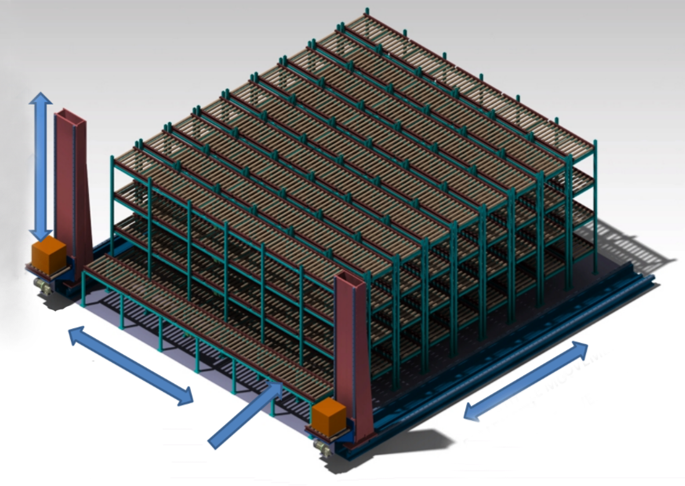
Scope of Work
- To store the product in a given matrix conveyor system.
- Product movement in & out of matrix conveyor will be via shuttle.
Solution
- Matrix conveyor system with 4 decks.
- Customized shuttle
Highlights
- Matrix conveyor system
- Control the input and output product in storage unit
- Compact storage area
Key Benefits
- High storage density.
- FIFO& FILO
02
2-Axes Robot for Pick and Place
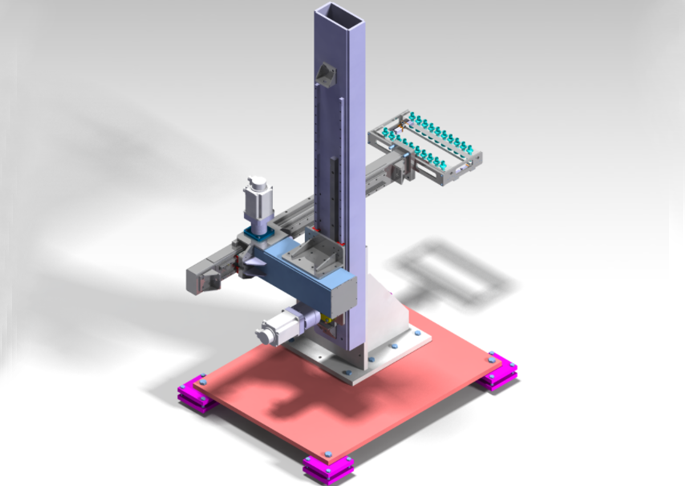
Scope of Work
- To pick & place set amount of bottle from molding m/c to conveyor
- 2- axes gantry.
Solution
- Gantry movement by servo with rack & pinion and LM rail.
- Product pick & Place By Pneumatic.
Highlights
- Customized picking finger.
- Servo controlled system.
- High speed with accuracy.
Key Benefits
- Customized picking finger.
- Reduced fixture changeover time.
03
De-Dusting Station
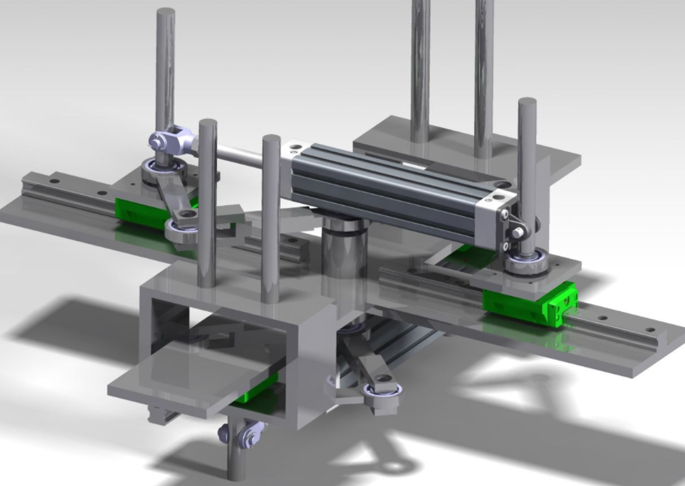
Scope of Work
- To Centralize and grip the product with 360 degree rotation for cleaning application.
Solution
- Using combination of centralizing unit with turntable to hold the product,
- dedusting is achieved by the robot.
Highlights
- Accurate product position
- Component in and out by roller conveyor.
- Turn table for product rotation.
Key Benefits
- Fully automated de dusting.
- No need for product centralization.
04
Bearing Cap Robotic Deburring
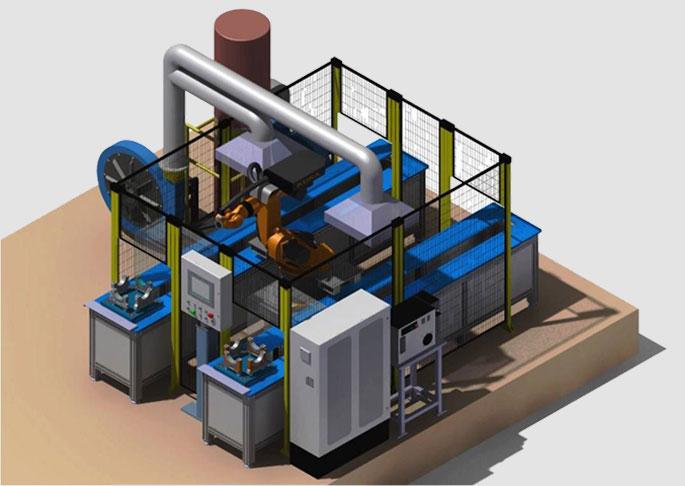
Scope of Work
- To de-burr the bearing cap using robot with slide.
- Identification of the Bearing cap variant for accurate deburring
Solution
- Quick change fixture for multiple variants.
- Bearing cap identification via vision system.
- Servo slide used for component traverse.
- Reduced cycle time using RH & LH slides.
- While deburring robot equipped with dust collector.
Highlights
- Deburring quality
- Maintaining chamfer
- Poka-yoke using vision
- Dust-free environment
Key Benefits
- Skilled operator not required
- Increased throughput.
- Reduced fixture changeover time
05
C-42 Gantry
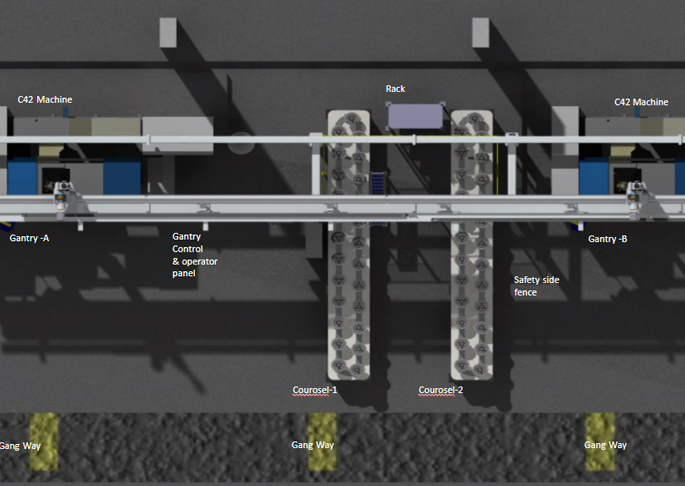
Scope of Work
- To handle both crown wheel and pinion based on the machine need.
- The machine should avoid waiting long for loading and unloading
- Positional accuracy to be built with 10 microns
Solution
- 27 meters long gantry with 6 axis each of the loaders comprising of 3 axes.
- Common gripper to accommodate more than 50 types of component.
- Controlled with Siemens 840 D SL and seamlessly interfaced with 2 machining centers having similar solution line controllers.
- Completely automated and unmanned system
Highlights
- Component variants identification is implemented with a vision system.
- Repeatability of 10 microns in both zones.
- 100% POKA YOKE compliance
- Auto corrections of position to accommodate component tolerance.
- Industry 4.0 compliance along with IIOT enabled
Key Benefits
- Avoids any manual errors
- Reduction of manpower from 4 persons to nil
- Increasing the through put of machine by 50%
06
Servo Press
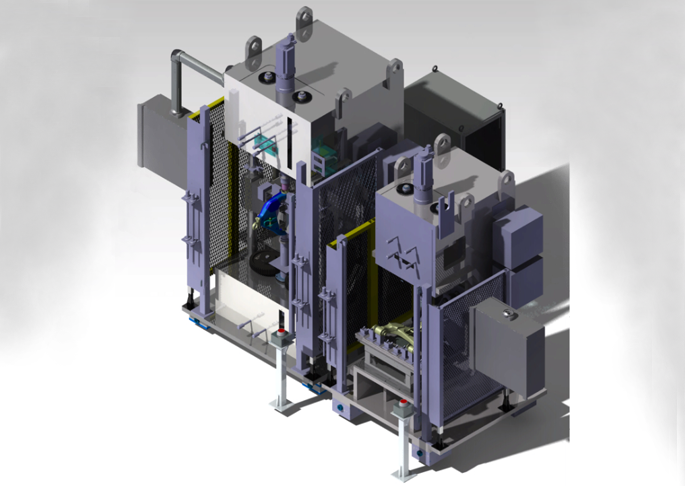
Scope of Work
- To Press the Bush & Ball joints into the arm using two press units.
- Pressing carried out by servo mechanism.
Solution
- Cycle time for each press is 30sec. & overall cycle time is 60sec.
- Common Fixture for various components.
- Controlled with Mitsubishi PLC & servo motor.
- Bush press top ram is 5tonne & Bottom ram press is 10tonne.
- Ball joint press is 5tonne.
Highlights
- Bush press is vertical dual ram (top & Bottom) press.
- Ball joint is single ram (top) press.
- 100% POKA YOKE compliance.
- Fixture configuration Quick change mechanism.
Key Benefits
- Avoids Hydraulic power pack.
- Easy maintenance.
- Error reports are automatically Generated for servo motors when required.
- To control & increase the Pressing quality.
07
Slat Conveyor
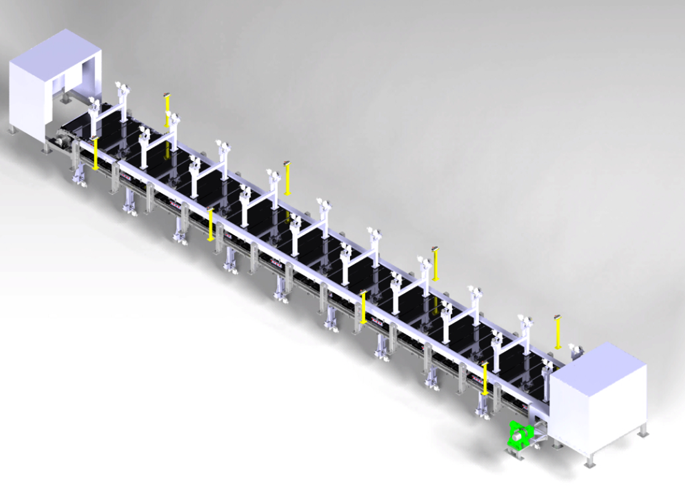
Scope of Work
- To Assemble child parts into front & rear axle.
- Axles are Banjo rear axle & winger, yodha 4X4, yodha4X2.
Solution
- Slat conveyor system for fix the fixtures & operators movement on slats to assembly the axels.
- This slat conveyor is with two layer pit one for structure mounting & and large pit was fixture movement.
- 20 Fixture assembled on the slats.
Highlights
- Operator can easily assembly the axles standing on the slat conveyor
- Universal fixture for all 4 variants.
- Quick change feature for all fixtures.
Key Benefits
- Continuous conveyor.
- Maintenance-free conveyor chain.
- To Increase the assembly part Quality.
08
Gear Box Assembly Line
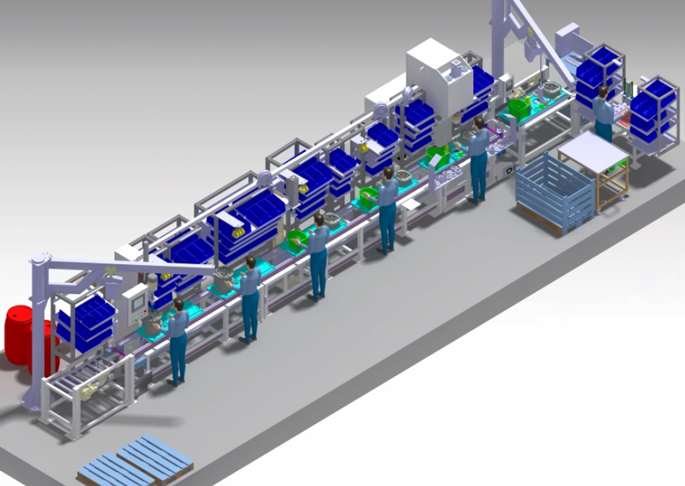
Scope of Work
- To assist in assembly for gearbox.
- This is a semi-automatic assembly line.
- Gear box AS45, AS 55 & AS 60.
Solution
- The overall dimension of the line is 1500x5000x3200mm
- The line is a semi-automatic assembly line.
- Universal fixture for across variants
Highlights
- 15tonne capacity servo driven press is in place for assembly of sub components in station #2.
- KAN BAN rack system is placed to assist the operator in assembling/ arranging the sub-components.
- Complete return line conveyor with lift table assist is in place for the fixture recirculation.
- Jig boom is in place for assisting the operator in loading/ unloading the component.
- 100% POKA YOKE compliance
Key Benefits
- IIOT 4.0 & Vision system for overall machine & component identification
- Increase the throughput by 10%.
- To control the quality of Gearbox.
09
Quench Press Assembly
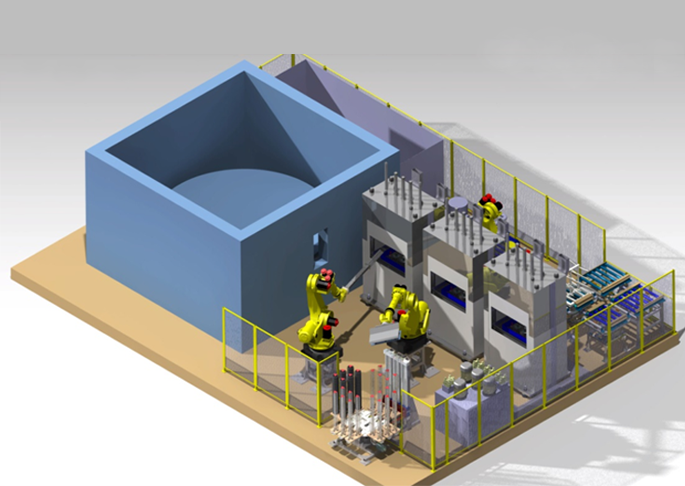
Scope of Work
- This project to handle the component from furnace to Quench press for the component Quenching.
- This is a fully unmanned Quenching Operation.
Solution
- Given robotic solution for furnace handling & press handling.
- Three quench press with three ram each press.
- Top ram capacity 1 ton. bottom ram capacity 10 ton.
- Component input by men through input carousel & output will be by output carousel
Highlights
- Closed quench oil system for clean floor environment.
- Compact quench presses.
- Quick change tooling's.
- Customized tray handling finger for furnace.
Key Benefits
- Finger biometric provided to avoid unnecessary access by other persons.
- Increase the throughput by 50%.
- To control the quality of Gear components.
10
FSP Palletizing
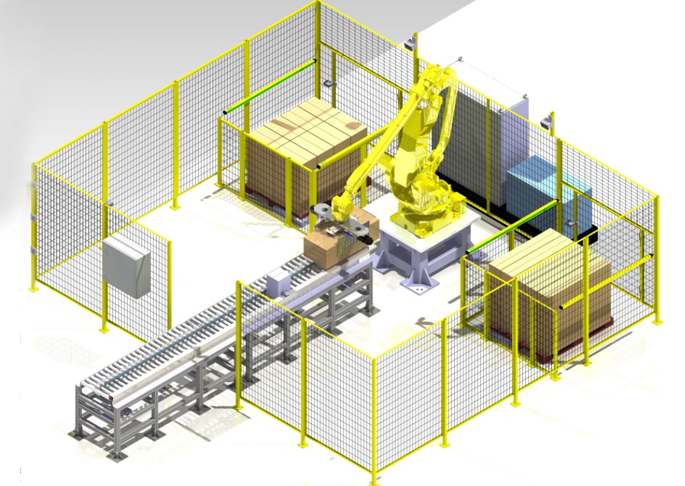
Scope of Work
- This project is to palletize the sealed carton box.
- Palletizing is a fully unmanned operation.
Solution
- Given various speed conveyors for singling.
- Automated box adjustment unit in conveyor.
- Twin palletizing station.
- Light curtain is provided to avoid unauthorized entry to palletizing zone.
Highlights
- Automated box adjustment mechanism in conveyor to accommodate various sizes box.
- Custom-designed universal gripper to handle the various size boxes.
- Twin palletizing station to aid continuous production.
Key Benefits
- Finger biometric to avoid unauthorized entry
- Robotized palletizing system.
11
End of Line Packaging
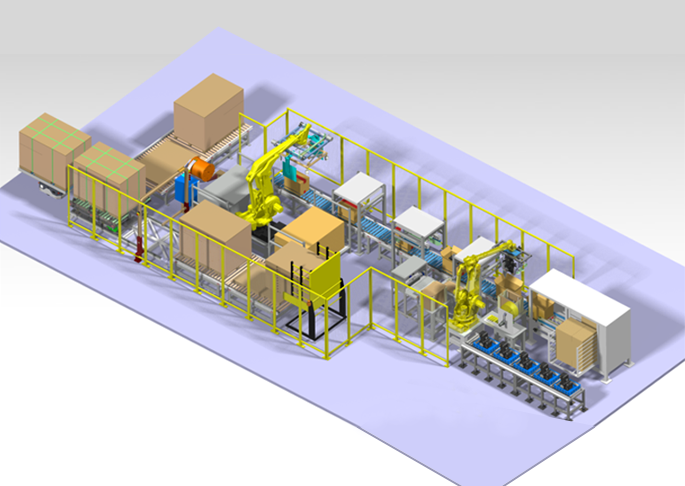
Scope of Work
- This project is for packaging and palletizing the Engine.
- This is a fully unmanned operation.
Solution
- Customized Grippers for packaging and palletizing.
- Dedicated case erector, carton sealing machine.
- Customized palletizing station and strapping station
Highlights
- Custom-designed gripper for engine handling.(engine pick & packaging & placing)
- Automated packaging, palletizing, and strapping process
Key Benefits
- Finger biometric to avoid unauthorized entry
- Robotized packaging, palletizing system
12
EOL Packaging for a Reputed Pharma Customer
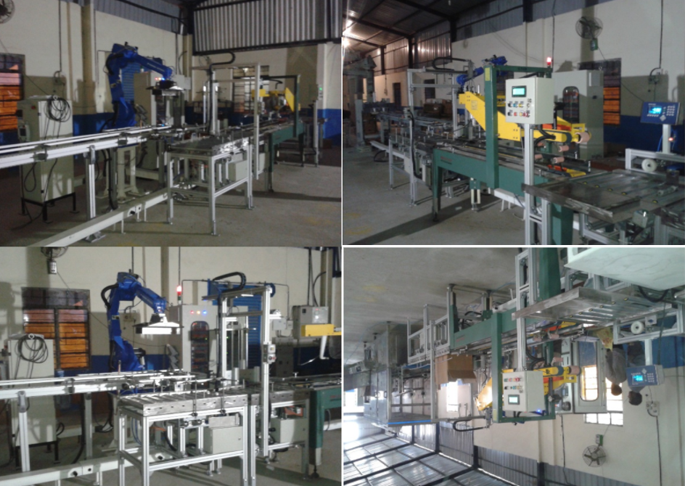
Highlights
- 150 cc to 2000 cc of capsule packing to be accommodated.
- The speed of the line should be at 1 carton a minute
- An individual carton will carry 120 bottles of 150cc as max and 12 bottles of 2000 cc as minimum
- The solution should be unmanned with traceability
- The solution comprises of case erector, bottom seal, pick and place by robot for needed matrix, leaflet dispenser, bottom sealer, Label print and applicate and real-time inspection with Vision.
- Completely unmanned solution to accommodate all the variants
- 27 variants accommodated
- Minimum setting time for variants change (Change over time less than 600 second)
- Real-time inspection before packing, over checking of mass with check weigh
- Machine works on ML platform
Key Benefits
- Reduction in manpower from 12 to 1
- With real time inspection the packed product qualifies for direct dispatch
- Reduced space from 1500 sq. meters of manual packing to less than 200 sq. meters
13
EOL Packaging for a Global Automotive OEM
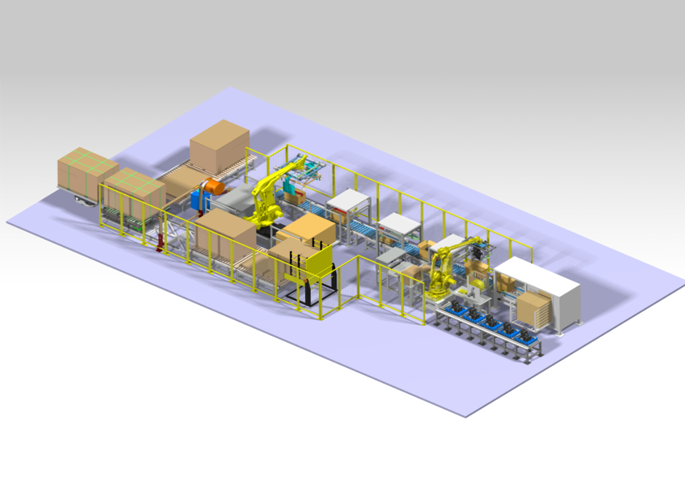
Highlights
- Siemens 1500 PLC is used as a master of control architecture.
- 12inch panel for Human machine interface
- Distributed modular to interface
- Drive controlled rotary tables for better positioning accuracy and variable speed.
- 6axis robot for engine handling
- High speed palletizing robot
- Compact robot controller with profinet interface.
- Custom designed EOAT to handle engine, stiffener’s and separator
- App based machine tracking and data recording
- Taurus is used to carry finished products
- All the stations will be working fully automatic
Key Benefits
- It is more efficient than humans.
- Increases Production speed
- Improves the quality of finished products.
- Manpower is reduced from 10 to 2
14
EOL Packaging for a Global Fire Protection System OEM
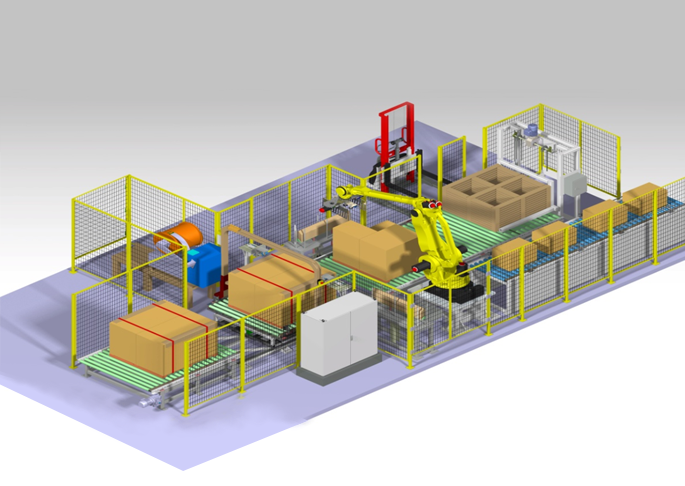
Highlights
- In station 10 operator will load the pallets on the auto pallet sacker through pallet truck then it is transferred to palletizing station through roller conveyer the pallet will be located by pneumatic cylinders.
- MCHX box will be fed through the existing feed conveyor
- I station 20 The robot will pick the MCHX box from conveyor using EOAT gripper and places it on the pallet. The robot will palletize the boxes as per the programmed matrix.
- After palletization, the robot will pick the corner stiffener using suction cups and places it on the top layer of the palletized box matrix. After placing corner stiffeners, the pallet will move into the shuttling conveyor for strapping.
- In station 30 shuttle conveyor will receive the pallet from the palletizing station and delivers it to the strapping station after strapping it delivers the pallet to buffer station
- In station 40 the strapped pallet will reach the buffer conveyor and the finished pallet can be unloaded from the buffer conveyor
Key Benefits
- Reduction of Manpower 4 to 1.
- Time consumption is reduced.
- Safety light curtains are provided to prevent any unauthorized intrusion
15
Warehousing for a Reputed Pharma Customer
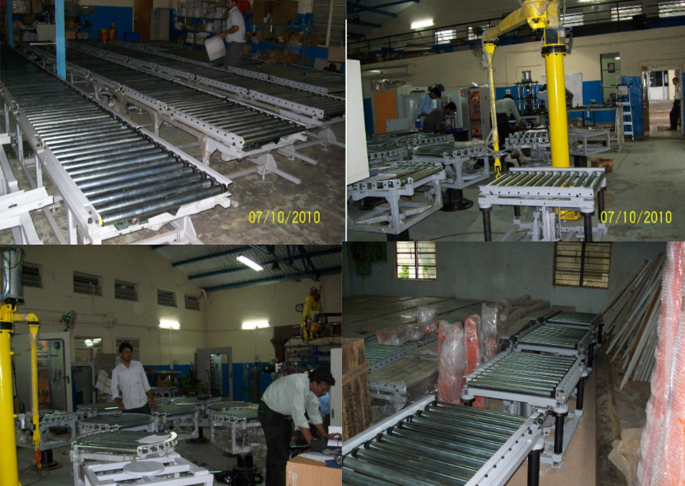
Highlights
- Automating of complete RM warehouse along with robotic de-dusting of pallets before it is transferred to the storage bay
- Comprises of accumulation type conveyors, turntables, Dock levelers, lift and transfer tables, Automated robotic de-dusting controlled by Machine Vision, product handling boom arm manipulators fitted with multiple product gripping arrangements, etc., The complete machine is SCADA controlled and the entire SCADA is indigenously programed by SSA
- Unmanned solution after unloading from the container till the parts are stored in warehouse.
Key Benefits
- Contactless handling of the RM is very essential in the oral drug manufacturing industry.
- Automated dedusting system which shall identify the different contours of products that is presented for dedusting with vision controls.
16
De-Dusting for a Reputed Pharma Customer
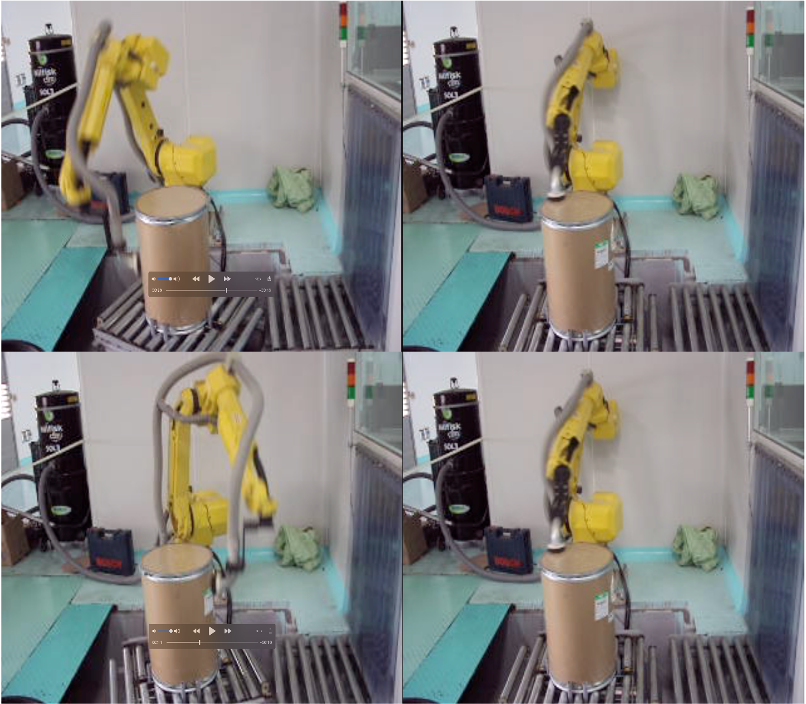
Highlights
- To thoroughly clean the pallets along with the products before it is stored in the raw material warehouse.
- Articulated arm robot with 6 axis is assembled with a high-power vacuum suction unit. The suction unit takes care of micro partials to be sucked which meets the customer’s acceptance criteria and compliance of 0.5 mg dust at external packing surface.
- 6 axis articulated arm fitted with high-power vacuum cleaner
- Vision is programmed to identify the parts and communicate to robot which ensures right trajectory and path.
Key Benefits
- Compliance is met at customer plant
Get in touch

